ZEISS Accelerates Semiconductor Package Failure Analysis by Orders of Magnitude with Crossbeam Laser FIB-SEM
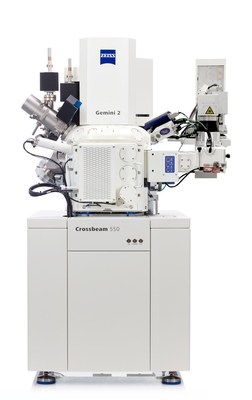
PLEASANTON, Calif., and OBERKOCHEN, Germany, Feb. 4, 2020 /PRNewswire/ — ZEISS today introduced the ZEISS Crossbeam Laser – a new family of site-specific focused ion beam scanning electron microscope (FIB-SEM) solutions that accelerate package failure analysis and process optimization for advanced semiconductor packages. Integrating a femtosecond laser for speed, a gallium ion (Ga+) beam for accuracy, and SEM for nanoscale-resolution imaging, the ZEISS Crossbeam Laser family provides package engineers and failure analysts with the fastest cross-section solution at the highest imaging performance, while providing minimal sample damage.
With its unique architecture, the ZEISS Crossbeam Laser family can rapidly cross section deeply buried package interconnects such as Cu-pillar solder bumps and through silicon vias (TSVs), as well as device back-end-of-line (BEOL) and front-end-of-line (FEOL) structures, in minutes instead of the hours or days of other approaches, all while minimizing artifacts and maintaining sample quality under vacuum. Besides failure analysis, the ZEISS Crossbeam Laser family enables structural analysis, construction analysis, reverse engineering, FIB tomography and transmission electron microscopy (TEM) sample preparation. Several ZEISS Crossbeam Laser systems have already been sold to major global electronics manufacturers.
New Approaches to Root Cause Failure Analysis Needed in 3D Packaging
The demand for increased miniaturization and higher interconnect density in mobile and high-performance devices has driven an explosion of innovations that enable fine-pitch and multi-chip architectures. These designs are not only shrinking packaging interconnects but are also increasingly driving them into the third dimension. At the same time, new types of defects buried deep within these packages are arising that can affect yield and reliability, and therefore must be quickly found and eliminated.
In the failure analysis workflow, non-destructive analysis is carried out as a first step toward optimizing package processes and improving package yields. Instruments such as the ZEISS Xradia Versa 3D X-ray microscope are used to visualize defect sites non-destructively, followed by destructive physical failure analysis (PFA) techniques to determine and resolve a failure’s root cause. Today, package interconnect and silicon BEOL dimensions are crossing over each other. Mechanical cross sections used commonly in PFA are now challenged to rapidly and accurately reach deeply buried structures and defects. In addition, the adoption of fragile materials in the silicon BEOL, such as extreme low-k dielectrics, leads to increasing numbers of cross-section-induced artifacts that are difficult to distinguish from true defects caused by chip and package interactions.
Plasma FIB (PFIB) is an alternative cross section approach but is 10,000x slower than a femtosecond laser. It is too slow to address ablation volumes of >0.5 mm3 in practical timeframes, as required in many package FA applications. Additionally, PFIB lacks the resolution needed for the highest-quality TEM sample preparation, and it induces ribbon artifacts in carbonaceous materials that are common in semiconductor packages. Standalone laser systems offer fast ablation but can have large heat-affected zones, increasing the likelihood of damage to the region of interest and increased polishing time to remove artifacts. Lack of integration with a FIB-SEM makes the FA workflow slower and less efficient, while risking oxidation artifacts due to atmospheric exposure prior to analysis.
“The packaging world has reached an inflection point where densities are approaching a million I/Os on a single silicon interposer, shrinking interconnects are starting to mirror the wafer fab and stacking is everywhere – in the device itself, among the package layers and within the printed circuit board. This makes fault isolation and failure analysis so much harder when a part fails,” stated Raj Jammy, Head of ZEISS Process Control Solutions (PCS) and Carl Zeiss SMT, Inc. “The ZEISS Crossbeam Laser family is designed to alleviate this pressure on the FA engineer, providing revolutionary time to results using a best-of-breed approach that combines speed, accuracy and high-resolution imaging all in a single instrument.”
The ZEISS Crossbeam Laser family offers an optimal PFA solution that dramatically improves total time to results while providing the highest imaging performance. Features include:
- Femtosecond laser for large volume removal with minimal artifacts (up to one cubic millimeter of silicon in only 30 minutes versus hours or days with other methods)
- ZEISS’s Gemini optics, which provide the highest image quality and analytics
- Ga+ FIB, which provides high-speed milling with 100nA combined with 500V fine polishing to reduce amorphization
- Accurate localized end pointing using FIB resolution (down to 3nm)
- Isolated laser chamber to segregate ablation contaminants from the main imaging chamber and maintain the highest-resolution imaging capability while keeping maintenance costs low
- Easy sample transfers between the FIB-SEM and laser chambers without breaking vacuum
- Laser preparation is suitable for many materials, including silicon carbide and glass
The ZEISS Crossbeam Laser combined with the ZEISS Xradia Versa XRM provide a powerful addition to standard FA workflows that will enable higher FA success rates and accelerated time to problem resolution.
For more information on the ZEISS Crossbeam Laser family, please visit: www.zeiss.com/pcs
About ZEISS
ZEISS is an internationally leading technology enterprise operating in the fields of optics and optoelectronics. In the previous fiscal year, the ZEISS Group generated annual revenue totaling more than 6.4 billion euros in its four segments Semiconductor Manufacturing Technology, Industrial Quality & Research, Medical Technology and Consumer Markets (status: 30 September 2019).
For its customers, ZEISS develops, produces and distributes highly innovative solutions for industrial metrology and quality assurance, microscopy solutions for the life sciences and materials research, and medical technology solutions for diagnostics and treatment in ophthalmology and microsurgery. The name ZEISS is also synonymous with the world’s leading lithography optics, which are used by the chip industry to manufacture semiconductor components. There is global demand for trendsetting ZEISS brand products such as eyeglass lenses, camera lenses and binoculars.
With a portfolio aligned with future growth areas like digitalization, healthcare and Smart Production and a strong brand, ZEISS is shaping the future of technology and constantly advancing the world of optics and related fields with its solutions. The company’s significant, sustainable investments in research and development lay the foundation for the success and continued expansion of ZEISS’ technology and market leadership.
With over 31,000 employees, ZEISS is active globally in almost 50 countries with around 60 sales and service companies, 30 production sites and 25 development sites. Founded in 1846 in Jena, the company is headquartered in Oberkochen, Germany. The Carl Zeiss Foundation, one of the largest foundations in Germany committed to the promotion of science, is the sole owner of the holding company, Carl Zeiss AG.
Further information at www.zeiss.com
Semiconductor Manufacturing Technology
With its product portfolio and expertise, the Semiconductor Manufacturing Technology segment of ZEISS covers a variety of key processes in the production of microchips. Its products include semiconductor manufacturing optics – notably lithography optics – as well as photomask systems and process control solutions for semiconductor manufacturing. Thanks to ZEISS technology, microchips are becoming increasingly smaller, more powerful, more energy-efficient and more affordable. The electronic applications of these ongoing enhancements enable global progress in many disciplines such as technology, electronics, communication, entertainment, mobility and energy. Semiconductor Manufacturing Technology is headquartered in Oberkochen. Other sites include Jena, Rossdorf and Wetzlar in Germany, as well as Bar Lev (Israel) and Pleasanton, CA and Peabody, MA (USA).
View original content to download multimedia:http://www.prnewswire.com/news-releases/zeiss-accelerates-semiconductor-package-failure-analysis-by-orders-of-magnitude-with-crossbeam-laser-fib-sem-300998364.html
SOURCE ZEISS