Meeting The Challenges Of Bioprinting
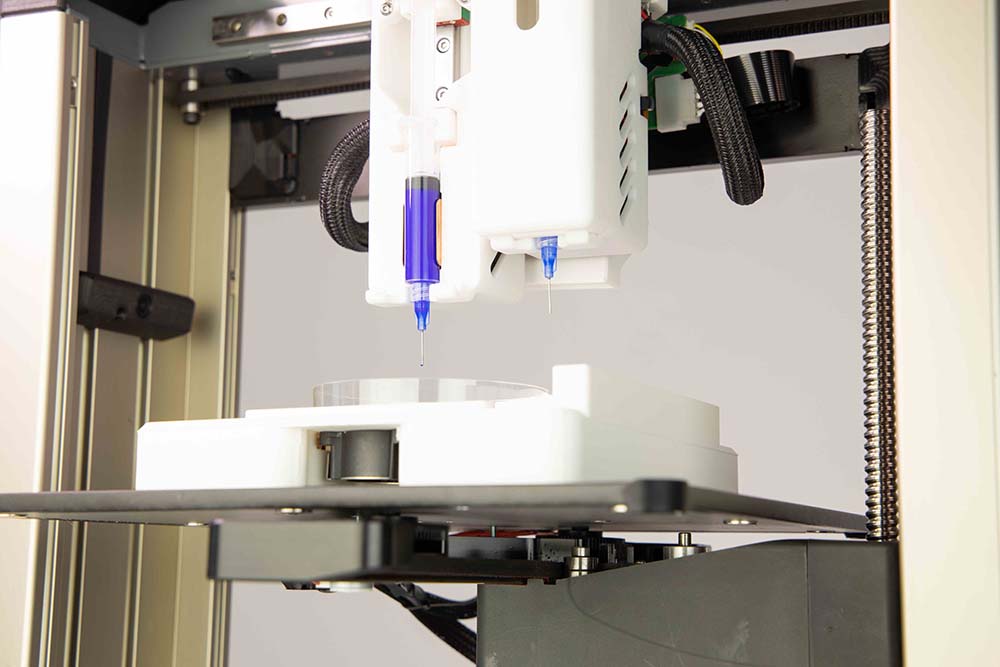
3D bioprinting offers opportunities such as testing treatment for diseases using artificially affected tissues, and through using bioink, it’s much easier to solve problems on a patient-specific level, promoting simpler operations. Within this context this article assesses the possibilities that exist for bioprinting, and looks at a newly introduced technology option that can provide highly reliable and cost-effective bioprinting options.
By Nadia du Plooy, Marketing Manager, FELIXprinters
With the growing demand for customized medical devices and pharmaceutical, 3D printing/additive manufacturing (AM) has begun to iron out a niche for itself in the medical and life sciences sectors. Throughout industry — but in the life sciences sector in particular — 3D printing has been truly disruptive, and some would say revolutionary, and it has promoted the manufacture of personalized implants and prosthetics, personalized and adjustable dosage forms for drug delivery, tissue engineering, and disease modeling.
But the use of AM in life science applications is not necessarily straight-forward. For example, the physiochemical and biopharmaceutical characteristics of active pharmaceutical ingredients (APIs) in drug formulations are extremely varied, and need to be considered alongside any proposed AM drug delivery solution. However, the over-riding demand for patient-centric drug and medical product development means that AM’s future is secured in the life sciences sector.
AM is now an established technology in the manufacture of models (phantoms) for surgical planning and training, implants and prostheses, patient specific anti-microbial wound dressings, and some novel forms of drug delivery, but a relatively less advanced area, and one in which FELIXprinters is working actively is in the field of bioprinting and so called “organs-on-chip”.

THE BIOPRINTING MARKET
The global 3D bioprinting market — currently valued at $965 million — is expected to grow at a CAGR of nearly 20% up to the mid 2020s, driven by increased healthcare demands, but also to overcome the supply bottlenecks and ethical issues associated with organ donation and tissue repair. Bioprinting also caters for the increased demand for customized patient-specific healthcare solutions, a trend that is only likely to accelerate moving forward.
The key stimulus behind AM driven bioprinting is to find a solution for organ / tissue rejection, and the requirement for lifelong immunosuppressant-based therapies. The area of regenerative medicine is constantly on the look out for mechanisms that allow for the fabrication of multi-layer soft biological materials such as living cells, and in this extremely exacting area of research, AM is finding a foothold.
Wilgo Feliksdal, Co-Founder of FELIXprinters explains, “To date, AM has been mainly used for the preparation of tissue construct such as blood vessels, liver, kidneys, heart tissue, cartilage, and bone. But all developments in this area of the use of AM requires a focus on the long-term viability of the “printed” cells, the control of cell proliferation so as to provide sufficient amount of functional and supporting cells and tissue homeostasis, and the requirement for tissues used in 3D printing to be able to survive pressure and shear stress during the 3D printing process, as well as contact with potentially harmful compounds.”
A NEW BIOPRINTING OPTION
With this in mind, FELIXprinters has recently launched its BIOprinter which has been developed on the chassis of the established FELIXprinters’ product line which includes the Pro and Tec series and the Pro L & XL machines. This means that at its heart is the tried and tested technology that has already been serving industry successfully for years.
The BIOprinter is characterized by key features that are specifically designed for medical, scientific, and research applications, including syringe cooling, print bed cooling and heating, a dual head system, easy syringe positioning (ergonomic access to the machine supports researchers in their work), and automatic bed levelling.
Guillaume Feliksdal, Co-Founder says, “The BIOprinter has been designed to be the ultimate bio research instrument but in a cost-effective package. It has been developed alongside the brightest minds in the bioprinting sector, and we partnered with training4crm and the Technical University of Denmark (DTU), and received funding from the European Union Horizon 2020 Programme to develop the BIOprinter. Uniquely, the BIOprinter combines dual sterilizable printheads which have a modular design for easy changeovers, and separate heads are available to print different bioinks at the same time. This integrates different material properties into a single scaffold structure.”
FELIXprinters has worked closely with the Technical University of Denmark (DTU) on bioprinting applications of 3D printing. Heading the research was Hakan Gürbüz, who explains the foundation of the work he is undertaking.
“The aim of the BIOprinter that we have developed with FELIXprinters is to allow the printing of scalable and perfusable hybrid scaffold structures, incorporating in the same structure at least two different material properties. For this purpose, we developed a hybrid 3D printing platform that enables the printing of 3D scaffolds with dual material properties (e.g. mechanical [soft/medium/hard], conductive or biological) and perfusable micro-channel networks, enabling the continuous supply of oxygen, nutrients, and necessary factors to cells growing and differentiating throughout the scaffold.”
3D printing has many advantages over conventional approaches to building scaffolds, not least its ability to position the cells precisely. Currently, there are three different classes of bioprinters that are used for deposition and patterning of biological materials including inkjet, micro-extrusion, and laser-assisted printing options. Each of these bioprinters has unique methods of depositing 3D cell structures with good resolution and viability. The FELIX BIOprinter is a micro-extrusion bioprinter, which makes it very simple to use.
Wilgo Feliksdal explains how micro-extrusion printers work. “Micro-extrusion bioprinters usually consist of a temperature-controlled biomaterial dispensing system, a stage capable of moving in the x, y, and z directions, light illuminated deposition area for photo-initiator activation, and a video camera for x-y-z command. Unlike other bioprinters, the micro-extrusion bioprinter generates a continuous string of bioink rather than many droplets of bioink by applying pressure — either pneumatically or mechanically — to force the bioink from a syringe.”
“These strings are deposited in 2-dimensional layers (as directed by the CAD-CAM software), and served as the base for the subsequent layers while the stage is moved up the z-axis, resulting in the formation of a 3D structure. Micro-extrusion bioprinters are compatible with a wider selection of bioink including high viscosity materials such as hydrogels, biocompatible copolymers, and cell spheroids.”
Effectively, the BIOprinter consists of an adaptable and flexible ecosystem to ensure that it can meet a wide range of researchers’ needs without generating unnecessary costs. One major advantage is the source control system which enables the user to use standard slicing software and make changes themselves if needed. Also, syringes are not restricted to expensive brand-specific or in-house produced products that essentially drive up operating costs. The machine instead has been designed to use a standard 5ml syringe, and standardized petri dishes and culture plates, so there are no limitations on auxiliary parts and materials.
The FELIX BIOprinter is appropriate for all types of bioprinting research, and is equipped with strong motors that can extrude a range of different viscosity of materials. In addition, the BIOprinter has been designed to be easily upgradeable, which means that the lifecycle of the machine can be extended without compromising quality, reliability, and productivity.
The platform has automatic bed levelling through the use of a unique probing system which results in a completely accurate first layer, which means a high quality end result. It also retracts with a highly precise motor for better dosage or materials and more accurate material flow versus alternative air pressure systems.
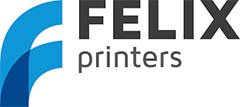
SUMMARY
Given its interdisciplinary nature, 3D bioprinting is accelerating at an ever-increasing rate. It’s exciting times, but we need to be careful to temper our expectations of this technology with the realities. The human body is incredibly complex, and trying to replicate the many things that it does is difficult. Those working in the field are making advances every day, in both the technology and in their understanding of how it can be used and improved. There is no doubt that the future of medicine will be very different with bioprinting involved, and the FELIX BIOprinter is perfectly positioned to cater for the spike in demand in the coming years as research in this area continues to expand.
CONTACT FELIXPRINTERS
Wilgo Feliksdal
T: +31 30 303 1387
wfeliksdal@felixprinters.com
https://www.felixprinters.com
ABOUT FELIXPRINTERS