COVID-19 Global Supply Chain Disruptions Continue
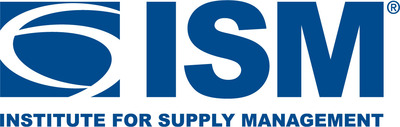
Institute for Supply Management® study second wave details virus’ adverse effects
TEMPE, Ariz., April 14, 2020 /PRNewswire/ — As a follow up to survey results released on March 11, today the Institute for Supply Management® (ISM®) released its second wave of research on COVID-19 impacts on businesses and their supply chains. Insights reflect input gathered by ISM® primarily from U.S.-based respondents between March 17 and 30.
Overall, response to the coronavirus is expected to substantially diminish organizational revenue and capital expenditures as impacts start to solidify within more organizations. Survey results note that almost one-half (47%) of respondents’ report reduced revenue targets of 22 percent on average, with 36% reporting a 27 percent reduction, on average, in CAPEX plans. However, some industries that expect increasing revenue include Food, Beverage & Tobacco Manufacturing (+8.8%), Wholesale Trade (+0.3%), and Management of Companies & Report Services (+17.5%).
The majority (57%) reported that demand for their products has decreased, on average, five percent. Alternatively, significant demand is hitting the Health Care & Social Assistance (+50%) industry, as evidenced by demand for personal protective equipment (PPE), even as revenue targets are adjusted by -30%.
“Domestic and global companies are in the midst of rapid shifts in supply chain planning, operations and inventory management to address coronavirus impacts,” said Thomas W. Derry, Chief Executive Officer of ISM. “The data suggests that even as companies adjust to supply disruptions – even anticipating normalizing supply conditions by the third quarter – they are expecting lower aggregate demand this year, which promises to be the most long-lasting impact of the virus outbreak.”
In early March more than 80 percent believed their organization would experience some impact due to COVID-19 disruptions. By the end of March, this increased to 95 percent of organizations who will be or have already been impacted by coronavirus supply chain disruptions.
Severe supply chain disruptions were experienced in multiple regions to varying degrees. In early March, six percent reported severe disruptions across their supply chains generally. By the end of March, severe disruptions were being reported in North America (9% for U.S. supply chains, 6% for supply chains elsewhere in North America), Japan and Korea (by 17% of respondents for each), Europe (by 24% of respondents) and particularly China (by 38% of respondents).
“We’re seeing further feedback that organizations who diversified their supplier base after experiencing tariff impacts, are potentially more equipped to address the effects of COVID-19 on their supply chains,” said Derry.
As the daily evolution of the virus’ impacts continues, global and domestic U.S. organizations are reporting the following primary supply chain impacts.
Lead Times
- Average lead times for inputs are at least twice as long as compared to “normal” operations, for Asian (222% for China, 217% for Korea, and 209% for Japan), European (201%) and domestically sourced inputs (200%).
- Compared to the end of 2019, 86% of respondents report that lead times for inputs from China have pushed out. Seventy-four percent report longer lead times for European inputs and between 34-44% report lengthening lead times for inputs sourced from North American countries.
- Through the end of April, 69% of respondents expect lead times to lengthen for U.S. inputs and 57% of respondents expect longer lead times from Canadian or Mexican suppliers. Europe is expected to be most impacted, with 85% of respondents expecting longer lead times for European inputs.
Manufacturing Capacity
- Domestic manufacturing is operating at 79% of normal capacity. Chinese and European manufacturing is at about one-half normal capacity, 53% and 50% respectively.
Inventory
- Firms report that operations in North America have or are likely have inventory to support current operations (U.S., 71%; Mexico/Canada 64%).
- Beyond April and into the end of Q2 and Q3, while uncertainty increases, respondent confidence remains relatively steady that inventory will be sufficient to support domestic and global operations, Europe being an exception.
- Nearly two-thirds (64%) of respondents say their firms’ input inventories have been adjusted in response to the coronavirus.
Talent
- In an already tight talent market, the majority of respondents (54%) report that their organizations will likely delay hiring this quarter, 33% will reduce hours, and 24% will reduce headcount.
- In late February, respondents reported that staffing levels in China stood at 56% of normal. By March, levels had recovered to 82% of normal.
The survey’s 559 respondents largely represent U.S. manufacturing (55%) and non-manufacturing (45%) organizations. Miscellaneous Manufacturing (11%), Fabricated Metal Products (6%), and Electrical Equipment, Appliances & Components (6%) were the top 3 manufacturing sub-sectors, with Health Care & Social Assistance (7%), Other Services (5%), and Utilities (4%) as the top 3 non-manufacturing sectors represented by respondents.
Eighty-five percent of the respondents come from organizations with annual revenues of less than US$10 billion, with 51% under US$500 million. Respondent roles range from emerging practitioner (4%), to chief procurement officer (6%), with 76 percent being experienced practitioners, managers, directors and vice presidents in a supply chain management role.
Another round of data collection will be conducted by ISM to continue to assess the coronavirus’ evolving global and regional supply chain implications. To access ISM’s dedicated resources and research regarding COVID-19, please visit: https://weareism.org/coronavirus-ism.html.
About Institute for Supply Management®
Institute for Supply Management® (ISM®) is the first and leading not-for-profit professional supply management organization worldwide. Its 47,000 members in more than 90 countries around the world manage about US$1 trillion in corporate and government supply chain procurement annually. Founded in 1915 by practitioners, ISM is committed to advancing the practice of supply management to drive value and competitive advantage for its members, contributing to a prosperous and sustainable world. ISM empowers and leads the profession through the ISM Report On Business®, its highly-regarded certification and training programs, corporate services, events and the ISM Mastery Model®. Its Manufacturing and Non-Manufacturing ISM Report On Business® are two of the most reliable economic indicators available, providing guidance to supply management professionals, economists, analysts, and government and business leaders. For more information, please visit instituteforsupplymanagement.org.
Contact: Jessica Boyd, 480.752.6276, ext. 3085
jboyd@instituteforsupplymanagement.org
View original content to download multimedia:http://www.prnewswire.com/news-releases/covid-19-global-supply-chain-disruptions-continue-301040385.html
SOURCE Institute for Supply Management